Jaw crushers are among the most essential machines used in mining, construction, and aggregate industries. Known for their robust design and reliable performance, these crushers have become the preferred choice for primary crushing operations. They work by breaking down large rocks and minerals into smaller, manageable sizes, which can be further processed or utilized in construction projects.
In this article, we will explore the mechanism of jaw crushers, how they operate, and their critical role in crushing materials efficiently. We will delve into the working principle, key components, types, and factors that influence the crushing process. Additionally, we will discuss the benefits of jaw crushers in material processing and why they are considered the cornerstone of aggregate production.
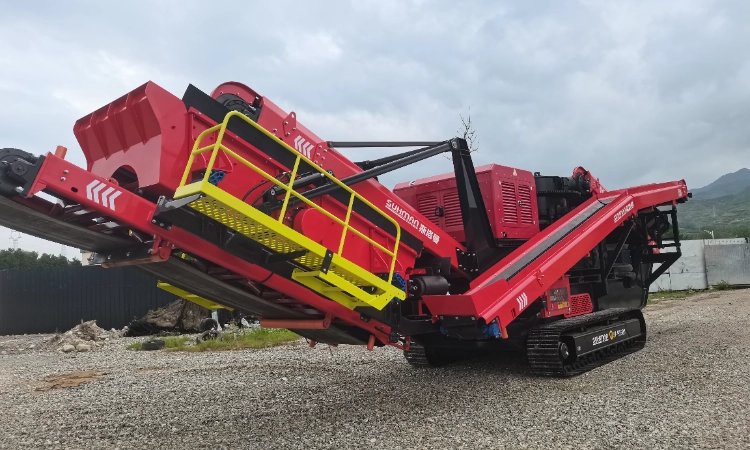
The Working Principle of Jaw Crushers
The basic principle behind jaw crushers is straightforward: a mechanical force compresses the material between two jaws, one of which is fixed and the other moves back and forth. When the material enters the crushing chamber, it is compressed and broken down into smaller particles. The crushing process continues as the material is forced through the narrow space between the jaws.
The jaw crusher mechanism involves two key movements:
- The swing motion of the moving jaw – This is the key element in the jaw crusher's functionality. The moving jaw moves toward and away from the fixed jaw, creating a narrowing gap where the material is crushed.
- The downward force exerted on the material – As the moving jaw swings, it pushes the material down, leading to further breakdown.
The Anatomy of a Jaw Crusher
A jaw crusher is composed of several key components that work in harmony to perform the crushing operation. Understanding these components helps explain how the mechanism functions efficiently.
- Fixed Jaw: This stationary part provides a stable surface for the material to be crushed against.
- Movable Jaw: The movable jaw swings back and forth in a controlled motion to compress the material against the fixed jaw.
- Toggle Plates: These components are responsible for transmitting the crushing force from the movable jaw to the stationary jaw. They also act as safety features, preventing damage to the crusher in case of an overload.
- Flywheel: This heavy component stores energy during the compression stroke and helps maintain a smooth operation by balancing the forces during the crushing cycle.
- Jaw Plates: The fixed and movable jaw plates are designed to withstand the wear and tear from the crushing process. They are typically made of high-quality manganese steel to enhance durability.
- Crusher Frame: The frame provides the overall structure for the jaw crusher, supporting all other components.
Table 1: Key Components of a Jaw Crusher
Component | Function |
---|---|
Fixed Jaw | Provides a stationary surface for the material to be crushed against |
Movable Jaw | Moves back and forth to crush material between the fixed jaw and itself |
Toggle Plates | Transfers the force from the movable jaw to the fixed jaw and acts as a safety feature |
Flywheel | Stores energy and helps balance the motion of the jaws |
Jaw Plates | Made from durable materials to withstand constant friction and crushing forces |
Crusher Frame | Supports all components and provides structural integrity for the machine |
How Jaw Crushers Break Down Materials
The crushing action of jaw crushers involves a series of stages that break down materials effectively. The material enters the crushing chamber, where it undergoes compression, shear, and impact forces. These forces work together to reduce the material's size in several stages.
- Compression: This is the primary mechanism of jaw crushers. As the movable jaw closes in on the material, it exerts compressive force, crushing the material into smaller pieces.
- Shear Force: Shear forces are generated when the material is squeezed between the fixed and movable jaw. These forces help further break down the material into finer fragments.
- Impact Force: In some cases, the material may also experience impact forces as it is thrown against the jaw plates, contributing to its breakdown.
Table 2: Types of Forces Involved in Material Crushing
Force Type | Description |
---|---|
Compression | The main force in jaw crushers, where the material is squeezed between the jaws |
Shear Force | Forces that help break down the material as it is compressed between the jaws |
Impact Force | Forces generated when the material collides with the jaw plates, assisting in fragmentation |
Factors Influencing the Performance of Jaw Crushers
Several factors can affect the efficiency and effectiveness of jaw crushers during the crushing process. These factors include:
1. Feed Size and Material Type
The size and type of material being fed into the crusher directly influence the crushing efficiency. Larger rocks or harder materials require more power to break down, which could affect throughput. Choosing the right jaw crusher for the material is essential for optimizing performance.
2. Jaws' Angle and Configuration
The angle between the movable and fixed jaw, also known as the crushing angle, determines how easily the material will pass through the machine. A larger crushing angle allows for more efficient crushing, while a smaller angle may result in higher wear and reduced performance.
3. Jaw Plate Design
The design of the jaw plates can significantly influence the wear life and crushing efficiency. Plates with a deep corrugated profile increase the material's exposure to crushing forces, improving performance. The quality and material of the plates are crucial to ensuring long-lasting use.
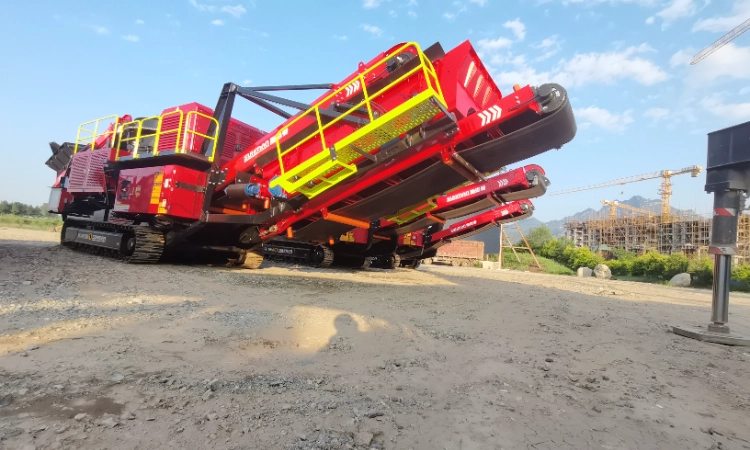
4. Machine Speed
The speed at which the movable jaw operates can impact the material’s reduction rate. Too high a speed might lead to inefficient crushing, while too low a speed could reduce productivity. Finding the right balance is essential.
Table 3: Factors Affecting Jaw Crusher Performance
Factor | Influence on Performance |
---|---|
Feed Size and Material | Larger or harder materials require more power and can affect throughput efficiency |
Jaws' Angle | Affects the crushing process, with steeper angles allowing more efficient crushing |
Jaw Plate Design | Deeper, more textured plates improve performance and longevity |
Machine Speed | Too high or too low speeds can lead to inefficient crushing and reduced productivity |
Benefits of Jaw Crushers in Crushing Materials
Jaw crushers offer a range of benefits that make them indispensable in material processing:
1. High Throughput Capacity
Jaw crushers are designed for high throughput, meaning they can process large amounts of material quickly. This is particularly important in industries where large-scale production is necessary.
2. Durability and Reliability
Given their robust design, jaw crushers can handle challenging conditions and continue to perform consistently for years. They are built to withstand harsh environments and heavy workloads.
3. Low Operating Costs
The simple design of jaw crushers translates to lower operating costs. These crushers require less energy compared to other types of crushers, helping to reduce overall expenses.
4. Versatility in Material Handling
Jaw crushers can handle a wide range of materials, from hard rocks to softer, more abrasive substances. This versatility makes them ideal for various industries, including mining, construction, and recycling.
Conclusion
Jaw crushers are indispensable tools in material processing, particularly in aggregate production. Understanding their mechanism helps explain why they are so effective in reducing large materials to smaller, usable sizes. Their efficiency, durability, and versatility make them a key component in crushing operations across various industries. By optimizing factors such as feed size, jaw plate design, and machine speed, operators can further enhance their performance.