Jaw crushers are a cornerstone of the crushing industry, providing vital functionality in the primary reduction of hard and abrasive materials. Over the years, the design and performance of jaw crushers have evolved through various innovations, significantly enhancing their efficiency, lifespan, and versatility. This article explores some of the latest innovations in jaw crusher design and examines how these changes have impacted their performance in real-world applications.
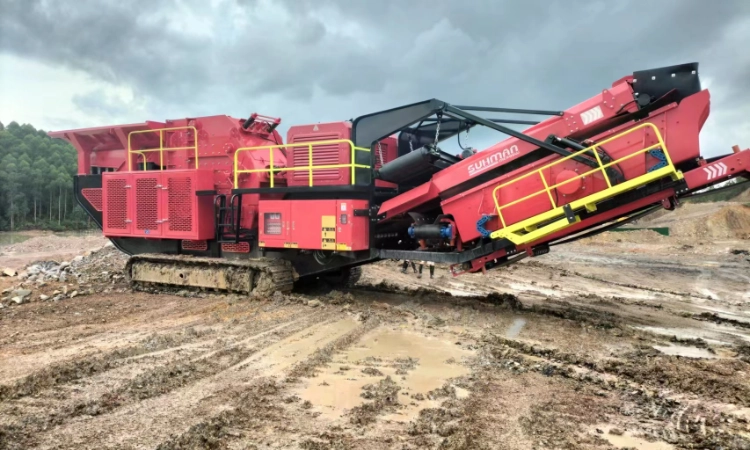
Introduction to Jaw Crushers
A jaw crusher is a heavy-duty machine used in mining, construction, and recycling industries to break down large stones and ores into smaller, more manageable pieces. Typically used as the first step in the crushing process, jaw crushers provide a primary reduction stage for various materials, including rock, gravel, and mineral ores. Their unique mechanism involves a pair of jaws – one stationary and one movable – that work together to compress and crush the material between them.
While the fundamental principle of the jaw crusher has remained largely unchanged over time, ongoing innovations have introduced various features designed to improve performance and reliability, as well as reduce maintenance costs and energy consumption.
Innovations in Jaw Crusher Design
1. Improved Crushing Chamber Design
The crushing chamber is one of the most critical components of a jaw crusher, as it dictates how effectively material is reduced. Over the years, advancements in chamber design have led to better material flow, increased throughput, and more efficient crushing.
Key Design Improvements:
- Deep and Steep Crushing Chambers: Modern jaw crushers feature deep and steep crushing chambers that enable the jaws to grip and compress material more effectively. This design reduces the amount of energy required to break the material and enhances the crusher’s capacity.
- Optimized Cavity Geometry: The geometry of the crushing chamber has been optimized to improve material throughput and minimize blockages. The use of computer simulations during the design process has allowed engineers to refine the shape and angles within the chamber for maximum efficiency.
- Manganese Steel Liners: Jaw crushers are often equipped with high-strength manganese steel liners, which are designed to withstand wear and tear from abrasive materials. These liners are available in various grades, offering superior wear resistance and prolonged service life.
Feature | Traditional Design | Modern Design |
---|---|---|
Chamber Depth | Shallow | Deep and steep |
Liner Material | Basic Steel | High-strength Manganese Steel |
Material Flow Efficiency | Moderate | High, optimized |
2. Hydraulic Adjustment Systems
In older jaw crushers, adjusting the closed-side setting (CSS) to change the size of the output material was a manual process that required downtime. Modern jaw crushers, however, are equipped with hydraulic adjustment systems that allow operators to adjust the CSS without having to stop the crusher. This innovation has greatly improved operational efficiency and flexibility.
Advantages of Hydraulic Adjustment Systems:
- Reduced Downtime: Operators can make adjustments on the fly, reducing the need for machine shutdowns.
- Faster Adjustments: Hydraulic systems allow for quicker and more precise adjustments compared to traditional mechanical systems.
- Increased Safety: The hydraulic system can be controlled remotely, reducing the need for personnel to be near moving parts, thus improving operator safety.
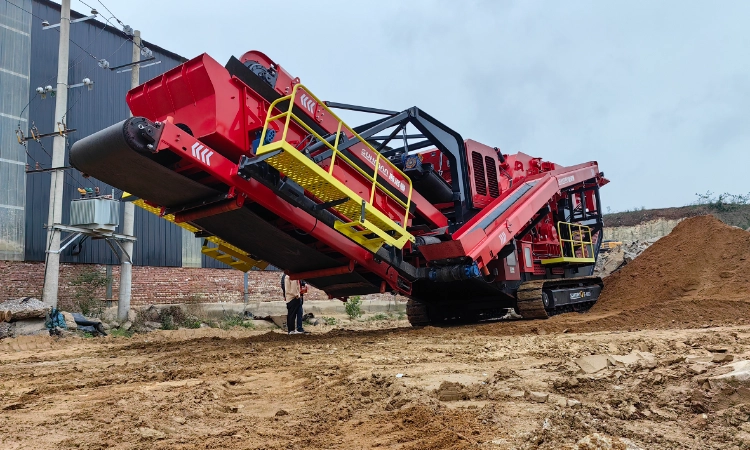
3. Advanced Control Systems
The integration of advanced control systems is another significant innovation in jaw crusher design. Modern crushers are often equipped with automation systems that monitor and control various operational parameters, such as feed rate, power consumption, and crushing force.
Features of Advanced Control Systems:
- Real-Time Monitoring: Sensors provide real-time data on various metrics, allowing operators to optimize crusher performance continuously.
- Predictive Maintenance: By monitoring wear patterns and vibrations, modern control systems can predict when maintenance is required, reducing the risk of unexpected breakdowns.
- Remote Monitoring and Control: Some jaw crushers can be controlled and monitored remotely, which allows for easier management of large-scale operations, especially in hard-to-reach or hazardous locations.
Feature | Traditional Jaw Crushers | Modern Jaw Crushers |
---|---|---|
Monitoring and Control | Manual | Automated and real-time |
Maintenance Prediction | Reactive | Predictive, with sensors |
Remote Operation | Not available | Available, with control systems |
4. Energy Efficiency Enhancements
Energy consumption is one of the largest operational costs for any crushing machine, and reducing energy usage is a key area of focus for modern jaw crusher designs. Manufacturers have integrated several features to minimize energy consumption while maximizing output.
Key Energy Efficiency Innovations:
- Variable Speed Drives: Modern jaw crushers come with variable speed drives that allow the operator to adjust the speed of the machine based on the material being processed. This helps optimize power usage, ensuring that the crusher operates efficiently in various conditions.
- Energy-Efficient Motors: Advanced electric motors and hydraulic systems are now more energy-efficient, using less power to achieve the same or better performance.
- Low Friction Bearings: Innovations in bearing technology, such as the use of low-friction bearings, help reduce power loss and heat generation during operation.
5. Durability and Reliability Improvements
Durability is an essential consideration for any crushing machine, as downtime and repair costs can significantly impact productivity. Manufacturers have implemented several design innovations to increase the longevity and reliability of jaw crushers.
Key Durability Innovations:
- Reinforced Frames: Modern jaw crushers are designed with reinforced frames made from high-strength steel, providing enhanced structural integrity and resistance to stress.
- Optimized Jaw Plates: The use of optimized jaw plate designs has improved the lifespan of these critical components. Various jaw plate profiles are available, each suited to different material types, reducing the rate of wear and tear.
- Advanced Seals and Lubrication: Newer models incorporate better sealing systems and advanced lubrication techniques, ensuring that the internal components remain protected from dust, debris, and moisture.
6. Increased Versatility
Modern jaw crushers are designed to be more versatile, allowing them to process a broader range of materials. By incorporating innovations such as interchangeable jaw plates and adjustable settings, jaw crushers can handle not only hard rocks but also softer materials like limestone, coal, and construction waste.
Versatility Features:
- Interchangeable Jaw Plates: Jaw crushers now offer easy-to-change jaw plates that can be swapped out depending on the material being processed. This feature allows crushers to handle a wider variety of tasks without sacrificing performance.
- Adjustable Settings for Different Materials: Modern jaw crushers allow operators to adjust the CSS to accommodate different materials, ensuring efficient processing for diverse applications.
Feature | Older Jaw Crushers | Newer Jaw Crushers |
---|---|---|
Jaw Plate Replacement | Manual and time-consuming | Quick and easy, interchangeable |
Adaptability for Various Materials | Limited | High, adjustable settings |
The Impact of Innovations on Performance
The innovations discussed above have had a profound impact on the performance of jaw crushers in various applications, including mining, construction, and recycling.
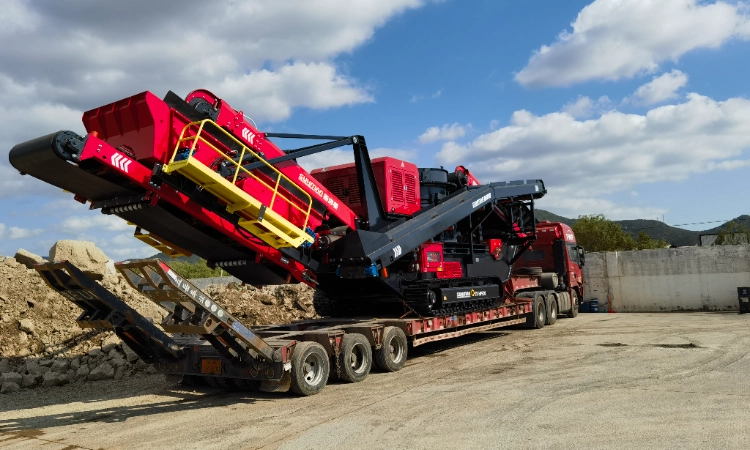
Increased Efficiency and Throughput
Improved crushing chamber designs and the integration of advanced control systems have resulted in increased throughput and more efficient material reduction. This means that jaw crushers are now capable of processing larger volumes of material in less time, ultimately reducing operational costs.
Reduced Maintenance Costs
Hydraulic adjustment systems, predictive maintenance capabilities, and increased durability features have reduced the frequency and severity of breakdowns, lowering maintenance costs. Operators can now make adjustments quickly and address potential issues before they lead to costly repairs.
Enhanced Energy Efficiency
The energy-saving features of modern jaw crushers, such as variable speed drives and efficient motors, have significantly reduced energy consumption, contributing to lower operational costs and a smaller environmental footprint.
Increased Versatility
Jaw crushers are now more versatile than ever, capable of handling a broader range of materials and applications. This makes them an even more valuable tool for companies involved in aggregate production, construction, and recycling projects.
Conclusion
The innovations in jaw crusher design have had a transformative impact on their performance. From improved crushing chamber geometry to hydraulic adjustment systems, energy efficiency enhancements, and increased durability, these advancements have made jaw crushers more efficient, versatile, and cost-effective. As these innovations continue to evolve, jaw crushers will remain a critical component in the crushing industry.