In the mining and quarrying industries, productivity is a key factor that influences the efficiency of operations and profitability. Jaw crushers are essential machines that play a pivotal role in enhancing productivity by facilitating the primary crushing of materials such as rocks, ores, and aggregates. Whether it’s a mining operation looking to extract raw minerals or a quarry that needs to produce construction aggregates, jaw crushers are indispensable for processing materials at the start of the crushing circuit.
This article will explore how jaw crushers improve productivity in mining and quarrying, providing an in-depth look at their role in material processing, the advantages they offer, and how their use can optimize the overall workflow. We’ll also highlight key factors that influence the performance of jaw crushers and discuss how to maximize their efficiency for the best results.
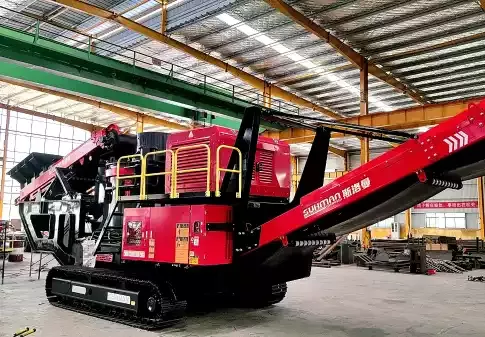
The Role of Jaw Crushers in Mining and Quarrying
Jaw crushers are used primarily for the first stage of material reduction in mining and quarrying. These machines work by applying compressive force to break down large rocks into smaller, more manageable pieces. The crushing action occurs when the movable jaw, attached to a swing arm, moves towards the fixed jaw, applying pressure to the material. As the material is crushed, it is further reduced until it reaches the desired size for further processing.
Jaw crushers are highly versatile and can be used for a variety of purposes, from breaking down large boulders in mines to processing construction aggregates in quarries. The ability to handle a broad range of materials, including hard and abrasive substances, makes jaw crushers essential for improving productivity in mining and quarrying operations.
Key Benefits of Jaw Crushers in Improving Productivity
1. High Throughput Capacity
Jaw crushers are known for their high throughput capacity, enabling operations to process large volumes of materials in a shorter period. This is especially important in mining and quarrying, where high quantities of raw material need to be processed regularly. By efficiently reducing large rocks to smaller sizes, jaw crushers can help speed up the overall production process.
The throughput capacity of a jaw crusher depends on factors such as the size of the machine, the design of the jaws, and the material being processed. Modern jaw crushers are designed with optimized features that allow for higher throughput rates without compromising the quality of the output.
Crusher Model | Maximum Feed Size (mm) | Output Size Range (mm) | Capacity (tons/hour) |
---|---|---|---|
Model A | 1000 | 100-200 | 200-300 |
Model B | 800 | 50-150 | 150-250 |
Model C | 1200 | 200-300 | 350-500 |
2. Reduced Downtime and Maintenance Costs
When jaw crushers are properly maintained, they can run for extended periods with minimal downtime. One of the most significant factors that contribute to increased productivity is the reliability of the equipment. Jaw crushers are designed to endure harsh conditions, and with regular maintenance, they can continue to function efficiently for long periods without significant repairs.
The use of high-quality materials in the construction of jaw crushers also helps reduce the frequency of wear and tear, minimizing downtime and maintenance costs. Components such as the jaws, bearings, and pitman arm are designed to handle high stresses, ensuring that the crusher operates consistently and smoothly.
3. Improved Material Size Control
Jaw crushers are engineered to deliver precise control over the final output size of the crushed material. In the mining and quarrying industries, achieving the right size of materials is critical for the next stages of processing, such as secondary crushing, screening, or transporting the materials.
With adjustable settings for the size of the discharge material, jaw crushers allow operators to optimize the size reduction process based on the material’s characteristics and the end-product requirements. This capability helps improve the overall efficiency of the entire production process.
Setting Option | Material Size (mm) |
---|---|
Coarse Settings | 100-150 |
Medium Settings | 50-100 |
Fine Settings | 20-50 |
4. Energy Efficiency
Modern jaw crushers are designed to be energy efficient, ensuring that operators can achieve maximum productivity while minimizing energy consumption. Energy efficiency is crucial in reducing operating costs, especially in large-scale mining and quarrying operations where crushers are used extensively.
Jaw crushers often feature advanced energy-saving technologies, such as optimized flywheel design and hydraulic assist systems, which reduce the amount of energy needed to crush materials. This not only lowers electricity consumption but also contributes to reduced carbon emissions and a more sustainable operation.
5. Versatility and Flexibility
Another significant advantage of jaw crushers in mining and quarrying is their versatility. These crushers are suitable for a wide range of materials, from hard and abrasive rocks to softer minerals. Jaw crushers can handle different materials like limestone, granite, basalt, and ores, making them ideal for various applications within the industry.
Their ability to handle a variety of feed materials means that jaw crushers can be used in multiple stages of the production process, from initial primary crushing to secondary or tertiary crushing. This flexibility allows for streamlined operations and greater productivity, as the same machine can be used for different tasks throughout the entire crushing cycle.
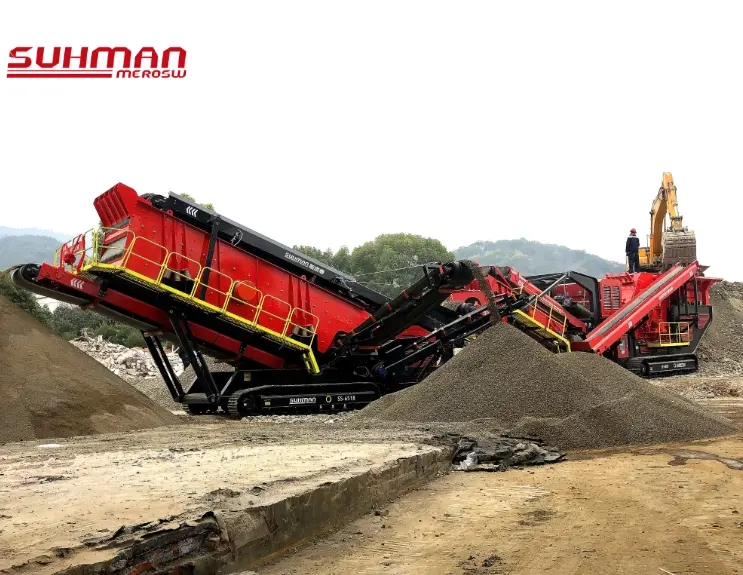
Factors That Influence Jaw Crusher Productivity
While jaw crushers offer numerous benefits for improving productivity, their efficiency is influenced by several key factors. By understanding these factors, operators can ensure that their crushers perform at optimal levels and achieve maximum output.
1. Crusher Size and Design
The size and design of the jaw crusher directly impact its throughput capacity and material handling efficiency. Larger jaw crushers are capable of handling bigger feed sizes and processing larger volumes of material. However, smaller crushers may be more suitable for specific applications where a compact design is necessary, or where space limitations are a concern.
2. Feed Material Characteristics
The hardness, abrasiveness, and moisture content of the feed material can significantly affect the performance of the jaw crusher. Harder and more abrasive materials require more energy to break down, which can slow down the crushing process. Additionally, wet or sticky materials may cause clogging in the crusher, leading to reduced efficiency.
3. Operational Parameters
Adjusting operational parameters such as feed rate, jaw gap, and crushing speed can have a significant impact on productivity. A well-calibrated jaw crusher will achieve the optimal balance between throughput and energy consumption, resulting in better overall performance.
4. Regular Maintenance
As with any heavy machinery, regular maintenance is essential for ensuring the continued productivity of jaw crushers. Worn-out components, such as jaw plates, bearings, and V-belts, should be replaced promptly to prevent operational disruptions. Routine inspections and lubrication will also help maintain optimal performance and reduce the likelihood of costly repairs.
Best Practices for Maximizing Jaw Crusher Productivity
To get the most out of your jaw crusher, here are some best practices that can help maximize its productivity:
- Regularly inspect and maintain the machine: Preventive maintenance will keep the machine running smoothly and reduce downtime.
- Optimize the feed size: Feed material that is too large may cause unnecessary stress on the machine, while material that is too small may reduce throughput.
- Adjust operational parameters: Fine-tuning settings such as jaw gap and crushing speed based on material type will help improve efficiency.
- Monitor wear and tear: Replacing worn-out parts before they cause major issues will help ensure continued productivity.
Conclusion
Jaw crushers play a vital role in improving productivity in mining and quarrying by providing high throughput, reduced downtime, and precise material size control. Their ability to handle a wide variety of materials, combined with energy-efficient designs and flexibility, makes them essential machines for any operation involved in the crushing process.