When it comes to crushing materials on-site for mining, construction, and demolition projects, mobile jaw crushers have become a popular choice due to their versatility, mobility, and ability to process materials quickly. Choosing the right mobile jaw crusher for your needs, however, can be a complex decision given the various factors involved, from the type of material you're processing to operational efficiency, cost, and maintenance. In this comprehensive guide, we will walk you through everything you need to know about selecting the right mobile jaw crusher, helping you make an informed decision based on your specific requirements.
Advantages of Mobile Jaw Crushers:
- Portability: Easy to move between sites and set up quickly.
- On-Site Processing: Materials are crushed directly at the extraction site, eliminating transport costs.
- Efficiency: Quick setup and fast processing times.
- Environmentally Friendly: Reduces emissions and energy consumption by eliminating transportation needs.
Key Factors to Consider When Choosing a Mobile Jaw Crusher
When choosing a mobile jaw crusher, several key factors will influence your decision. These include:
- Type of Material: Different crushers are better suited for specific materials such as hard rocks, soft rocks, or recycling materials.
- Capacity and Throughput: The crusher's capacity to handle large volumes of material per hour will be a critical factor, depending on the size and scale of your operation.
- Size and Weight: A larger, heavier crusher may offer higher capacity but could be harder to transport.
- Power Source: Mobile crushers may come with diesel, hybrid, or electric power options. The choice will depend on the availability of fuel and environmental considerations.
- Cost of Ownership: This includes the initial purchase cost, maintenance costs, and operational costs such as fuel consumption.
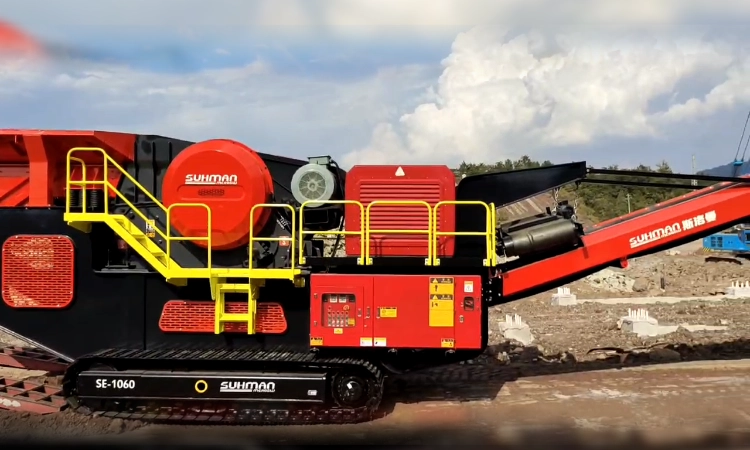
Let’s explore these factors in greater detail.
1. Material Type
The first consideration when selecting a mobile jaw crusher is the type of material you will be processing. Different jaw crushers are designed to handle specific types of materials effectively.
Table 1: Material Types and Corresponding Crusher Features
Material Type | Recommended Crusher Features | Considerations |
---|---|---|
Hard Rock | High-capacity, durable components | May require more power and frequent maintenance |
Soft Rock | Lighter, less heavy-duty design | Easier to crush, but may need more frequent adjustments |
Recycling Waste | Designed for mixed materials, energy-efficient | Suitable for reducing construction debris and recycling materials |
Mobile jaw crushers for hard rock need to be equipped with durable components, as they must withstand high pressures and abrasive materials. For soft rock, crushers may have less complex designs and need fewer robust features. When dealing with recycling waste, mobile crushers are designed to handle mixed materials and maximize efficiency, particularly in urban or demolition projects.
2. Crusher Capacity and Throughput
The capacity of a mobile jaw crusher directly impacts your operational efficiency. Crusher capacity is usually measured in tons per hour (TPH) and can vary significantly depending on the size and model of the crusher.
Table 2: Mobile Jaw Crusher Capacities
Crusher Model | Capacity (TPH) | Suitable Applications |
---|---|---|
Small-Scale Model | 50–150 TPH | Small construction or recycling sites |
Mid-Range Model | 150–350 TPH | Medium-sized quarries and mines |
Large-Scale Model | 350–800 TPH | Large mining operations and quarries |
For small to medium-sized operations, a small-scale mobile jaw crusher with a capacity of 50–150 TPH may suffice. However, for larger-scale operations, you’ll want a mid-range or large-scale model that can handle higher throughput, ensuring you meet the demands of high-volume crushing.
3. Size and Weight Considerations
Size and weight are important factors to consider, especially when transportation and mobility are essential. Larger crushers often have higher throughput capacities but may be harder to move, requiring larger transport vehicles and more logistical planning.
Table 3: Mobile Jaw Crusher Sizes and Transport Considerations
Crusher Model | Dimensions (L x W x H) | Weight (kg) | Transport Requirements |
---|---|---|---|
Small Model | 10 x 3 x 4 meters | 20,000–30,000 | Easy to transport with a standard truck |
Mid-Range Model | 12 x 4 x 5 meters | 40,000–60,000 | Requires larger transport vehicles |
Large Model | 14 x 5 x 6 meters | 70,000+ | Heavy-duty transport needed |
Smaller models are ideal for jobs where mobility is a key factor, while larger crushers provide higher productivity at the cost of mobility.
4. Power Source Options
Power sources are an important consideration, particularly when it comes to fuel efficiency and environmental impact. Mobile jaw crushers typically come with three main power options: diesel, hybrid, and electric.
Table 4: Mobile Jaw Crusher Power Options
Power Source | Advantages | Disadvantages |
---|---|---|
Diesel | Independent of power grid, widely available | Higher fuel consumption, more emissions |
Hybrid | Combines diesel and electric power, fuel-efficient | More complex system, higher upfront cost |
Electric | Lower environmental impact, energy-efficient | Dependent on access to electricity, limited mobility |
For environmentally conscious operations, electric-powered mobile jaw crushers offer a great alternative, while hybrid models can help balance fuel efficiency with mobility. Diesel-powered crushers are still the most widely used due to their versatility and reliability.
5. Cost of Ownership
The cost of owning a mobile jaw crusher encompasses more than just the initial purchase price. Factors like maintenance, fuel consumption, and operational efficiency also play an important role in long-term cost considerations.
Table 5: Cost Breakdown for Mobile Jaw Crushers
Cost Factor | Diesel Model | Hybrid Model | Electric Model |
---|---|---|---|
Initial Cost | Lower | Higher | Moderate |
Fuel Costs | Higher | Lower | Minimal |
Maintenance | Moderate | Moderate | Low |
Operational Costs | High | Moderate | Low |
Hybrid and electric models may have a higher initial cost but could save money in the long run due to lower fuel and maintenance expenses. Diesel models are generally more affordable upfront but come with higher operational costs.
How to Choose the Right Mobile Jaw Crusher for Your Project
Now that we've covered the key considerations, how do you choose the right mobile jaw crusher for your specific needs?
1. Determine Your Project Requirements
Start by evaluating the material type you will be processing, the capacity you need, and the power source that fits your operation. If you’re working in a remote location without access to electricity, a diesel-powered model may be the best choice. If sustainability and low fuel consumption are a priority, hybrid or electric models are worth considering.
2. Evaluate Size and Weight
Consider the logistical challenges involved in transporting the crusher to and from your site. If you have limited space or need to move the crusher frequently, a smaller, lighter model may be the best option.
3. Cost Analysis
Conduct a comprehensive cost-benefit analysis by considering not only the purchase price but also long-term fuel, maintenance, and operational costs. While an electric model might have a higher upfront cost, its lower operational costs could make it more economical in the long run.
Conclusion
Choosing the right mobile jaw crusher involves understanding your specific project requirements, material types, throughput needs, and logistical considerations. Whether you opt for a diesel, hybrid, or electric model, each crusher type has its advantages, and the best choice depends on factors like fuel efficiency, mobility, and environmental impact.