Jaw crushers are essential equipment in many industries, particularly in mining, construction, and demolition, where they are used for crushing large rocks and materials into smaller, manageable sizes. As with any heavy machinery, jaw crushers face a variety of operational issues that can impact their performance, efficiency, and lifespan. Understanding these issues and knowing how to address them is crucial for maintaining a high level of productivity.
In this article, we will examine some of the most common issues that jaw crushers encounter and provide practical solutions for overcoming them. Whether you are a seasoned operator or a new user, these insights will help you improve the performance of your jaw crusher and avoid costly downtime.
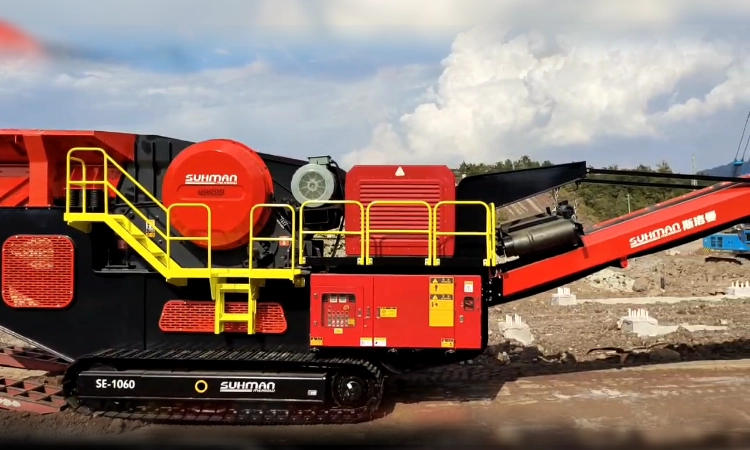
1. Excessive Wear of Jaw Plates
Problem:
One of the most common issues in jaw crushers is the excessive wear of jaw plates. The jaw plates are subjected to intense pressure and friction as they crush materials, which causes them to wear down over time. This can lead to decreased efficiency and increased maintenance costs.
Solution:
To minimize wear, ensure that the jaw plates are made from high-quality, wear-resistant material such as manganese steel. Regularly inspect the jaw plates for signs of wear and replace them before they are worn down too much. Additionally, you can adjust the feed size to ensure that material entering the crusher is not too hard or too abrasive, which can speed up wear.
Jaw Plate Material | Characteristics | Recommended Application |
---|---|---|
Manganese Steel | High resistance to wear, durable | High-abrasion materials like granite and basalt |
High Carbon Steel | Resistant to shock and impact | Applications requiring high strength and hardness |
Alloyed Steel | Increased toughness, less prone to cracking | Moderate abrasion and impact situations |
2. Clogging and Blockages
Problem:
Clogging and blockages in the jaw crusher can significantly reduce its productivity. These issues occur when material accumulates in the crusher, preventing smooth operation. This can be caused by moist or sticky materials, oversized rocks, or improper feed settings.
Solution:
To avoid clogging, ensure that the feed material is consistent and dry, particularly when dealing with wet or sticky materials. Additionally, avoid overloading the crusher by maintaining a balanced feed rate. Installing a vibrating feeder can help control the flow of materials and prevent blockages. It is also important to use a proper scalper or screen before feeding the material into the jaw crusher to remove larger particles and avoid clogging.
Material Type | Potential for Clogging | Suggested Solution |
---|---|---|
Wet Material | High | Pre-screen or use a de-watering system |
Oversized Rocks | High | Use a primary crusher with a larger feed size capacity |
Sticky Material | Moderate | Add a scalper or vibrating feeder for better material flow |
3. Vibration and Noise Issues
Problem:
Excessive vibration and noise are common in jaw crushers and can be indicative of several underlying issues. Vibration can be caused by an imbalanced or improperly aligned machine, while excessive noise can signal problems with the bearings, jaws, or other mechanical components.
Solution:
To minimize vibration and noise, ensure that the crusher is properly aligned and securely mounted on a stable surface. Inspect the bearings and lubricate them regularly to prevent friction and wear. If unusual noise persists, it may be necessary to replace damaged or worn-out components, such as the flywheel or bearing housings. Additionally, using vibration dampeners can help reduce operational noise and vibrations.
4. Poor Product Size Control
Problem:
Another common issue in jaw crushers is poor product size control. If the crusher is not set up properly or the material characteristics change, the size of the crushed product may not meet specifications. This can cause inefficiencies and result in further processing issues.
Solution:
To ensure consistent product size, regularly check the setting of the jaw crusher to ensure it is properly adjusted. Jaw gap settings should be calibrated based on the feed material's characteristics and the desired final product size. Investing in a crusher with adjustable settings and an integrated control system will help operators optimize product size control. A high-quality screening system downstream can also help ensure the product meets desired specifications.
Jaw Gap Setting | Material Type | Resulting Product Size |
---|---|---|
Wide | Soft Materials | Larger product sizes |
Narrow | Hard Materials | Finer, more consistent sizes |
5. Unusual Power Consumption
Problem:
Jaw crushers can sometimes experience excessive power consumption, which not only affects efficiency but also leads to higher operational costs. This can be caused by various factors such as an overloaded crusher, incorrect settings, or poor maintenance.
Solution:
To reduce power consumption, operators should avoid overloading the crusher by maintaining an optimal feed size and controlling the feed rate. Regular maintenance is essential, as worn-out components such as bearings, flywheels, or the eccentric shaft can increase friction and power consumption. Upgrading to energy-efficient models that incorporate modern technologies, such as hydraulic assist or energy-saving flywheel designs, can also help reduce energy consumption.

6. Bearing Failures
Problem:
Bearing failure is a common issue that can cause significant downtime in jaw crushers. Bearings are critical components that support the crusher’s moving parts, and when they fail, it can lead to costly repairs and productivity loss.
Solution:
Regular maintenance and lubrication are crucial to extending the lifespan of bearings. Ensure that the bearings are properly aligned and lubricated according to the manufacturer’s specifications. Check for signs of wear or damage, such as excessive noise, heat, or vibrations, and replace bearings before they fail. Using high-quality bearings and choosing crushers with robust bearing systems can also minimize the risk of failure.
Bearing Type | Maintenance Requirements | Failure Signs |
---|---|---|
Roller Bearing | Regular lubrication | Overheating, excessive vibration |
Ball Bearing | Periodic inspection | Noisy operation, uneven wear |
Split Bearing | Easy replacement | Loss of smooth rotation |
7. Inconsistent Crushing Force
Problem:
Inconsistent crushing force can lead to reduced efficiency and uneven wear on the jaw plates. This issue is often caused by an improperly adjusted jaw gap, wear on the toggle plates, or problems with the hydraulic or mechanical systems.
Solution:
To address inconsistent crushing force, ensure that the jaw gap is set correctly based on the material being processed. If hydraulic systems are involved, check for pressure inconsistencies and repair or replace any faulty components. Regularly inspect toggle plates for wear and replace them if necessary. Using crushers with advanced automation systems can also help monitor and adjust crushing force in real-time, ensuring consistency.
8. Overheating
Problem:
Overheating is another common issue in jaw crushers, often caused by insufficient lubrication, overloading, or operating in extreme conditions. Overheating can lead to premature wear, damage to components, and even failure of the machine.
Solution:
To prevent overheating, ensure that the crusher is properly lubricated, and the cooling system is functioning effectively. Avoid overloading the crusher and ensure that it operates within its recommended capacity. If the crusher operates in high-temperature environments, consider installing additional cooling systems or selecting crushers designed for such conditions.
Conclusion
Jaw crushers are an integral part of many industrial operations, and understanding the common issues that can arise and how to address them is essential for maintaining optimal performance. By addressing wear and tear, minimizing blockages, ensuring proper alignment, and performing regular maintenance, operators can significantly extend the lifespan of their jaw crushers and maintain productivity levels.
At SUHMAN, we specialize in the design and manufacture of high-quality jaw crushers that are built to last. Our products are engineered for reliability, efficiency, and ease of maintenance, helping your operation run smoothly. If you need a high-performance jaw crusher, don’t hesitate to contact us today and learn more about our products.